Concrete, Wood, Steel, in New Construction
Most construction (even a "steel" basement) involves concrete at least for the foundation and footings. Builders often use wood for above-ground ("stick-built") for many reasons but wood has drawbacks too. Concrete is rot resistant, flame resistant, and provides a "thermal mass" that moderates indoor temperatures by storing and releasing heat (the mass should be inside the insulation envelope). Concrete is now used more often for above-ground construction, partly because of forms, stamps, and stains that can mimic the look of other materials.
Decorative concrete floor:
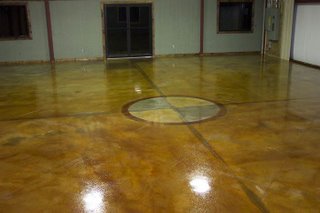
Concrete spans must be relatively short but there are even concrete roof systems now. For walls, there are now many products, from the old "cinder blocks," to the Concrete Masonry Units (CMU), to a familiar cast-in-place (CIP) poured wall, to new prefabricated insulated forms (instead of a wooden frame for a mold, insulated panels form the mold and remain as insulation), to prefabricated concrete panels. All have pros and cons. Small blocks handle easily but every seam is a potential leak. Large pieces are harder to handle and might limit design choices. Poured monoblocs have few seams but typically require the careful construction of temporary wooden walls for the mold. The new Structural Insulated Panels (SIP) and Insulated Concrete Forms (ICF) typically have higher initial cost and might need to add finished surfaces to both sides.
I would like to find a good review of cost effectiveness of various methods, including construction cost per square-foot per R value of insulation.
See: California Fire-Proof Concrete Roofs
1 Comments:
Concrete, Wood, Steel, in New Construction is the real deal! Best. Product. Ever!
Post a Comment
<< Home